Hello!
- OUR DADS always taught us - that using the right tool for the job produces the best results. In addition, we all know how using the wrong tool produces well, less than the best results (Crescent wrench to hammer in a nail is bad!)
Somewhere along the line, everyone who has ever held a wrench in his or her hand has attempted to use a 7/16 inch wrench (or socket) on a 10-millimeter bolt head. I know I have. You know you have. How’d that work out for you?
Yeah, you might have gotten away with it when tightening the plastic cover on your lawn mower… But I bet you can remember a somewhat more critical application and the swear words you uttered each time you rounded off a corner on the bolt head, the wrench slipped and you knuckles bled.
“Close enough” is not good enough in most repair situations. The difference between 10 millimeters and 7/16 of an inch is only 0.04 inches. Not very much – unless the situation calls for precision, accuracy and a successful repair.
By now, some of you are reading this and congratulating yourself for learning this lesson early – and have moved on to making “professional” repairs. You always use the right tool and take pride in the precision and accuracy of your repairs. You always use the right tool; but is your tool always right?
Let’s use the same math we learned earlier. This time, we will apply the lesson about precision toward working with one of the (potentially) most precise tools in your toolbox, your torque wrench!
If you are reaching for a torque wrench to perform a repair, you already realize that an accurate application of torque to several fasteners is absolutely critical to completing a successful repair.
(Please disregard if performing government work…)
Maybe you are staring at high pressure 12 bolt flange? Or maybe you are staring at thirty-four new cylinder head bolts – that must be torqued in a specific sequence, torqued in three separate steps, to a final torque value of 65 ft./lbs. You know this job is critical. You might be performing an expensive repair for a retail customer and offering a long-term warranty on your work; or, you may be trying to squeeze the last few horsepower out of your own Chevy small block, project car.
So, ask yourself, is 65 ft./lbs. of final torque what you want to achieve? Will 55 ft./lbs. be just as good? Is 75 ft./lbs. okay? What if all thirty-four bolts are at least somewhere in between 55 and 75 ft./lbs?
A true profession already knows the answer to these questions. However, does he know if his torque wrench is accurate enough to deliver those results? What about you? Do you know how accurate your torque wrench is?
Your wrench might be a brand name tool. It may have been expensive. Somewhere, the packaging and paperwork may state that it is capable of +/- 3% accuracy. It may even have come with an initial (time of manufacture) certificate of accuracy. When did you buy that torque wrench… ?
The point of the matter and the real question is: Do you really know if the readings shown on your torque wrench are right, or just close to being right?
Some FACTS to consider:
• - Brand name and purchase price do not guarantee the accuracy of a torque wrench
• - New torque wrenches can be out of specification right out of the box
• - Certificates of calibration on a new torque wrench may not guarantee accuracy
• - Use of a torque wrench affects accuracy
• - Misuse of a torque wrench affects accuracy
• - Disuse (prolonged or incorrect storage) of a torque wrench affects accuracy
• - Abuse (have you ever accidentally dropped it?) of a torque wrench affects accuracy
Learning these facts, do you really know if your torque wrench is accurate? You were professional enough to purchase a torque wrench and to use one on all critical installations. Knowing that critical installation success starts and ends with torque tool accuracy, here are some BEST PRACTICES regarding torque tool accuracy certification.
Have your torque tool tested (and recalibrated if necessary) as soon as possible after purchase. - Production line testing may not be as robust or accurate as individual tool testing performed in an accredited laboratory.
Choose an independent lab for testing, repair and calibration.
- You may find the torque tool manufacturer’s testing services to be less critical or stringent when measuring their own product.
Choose an accredited lab.
- ISO17025 is the top level laboratory standard available internationally. Additionally, A2LA is the most recognized and meticulous accrediting body for that standard. If a laboratory has not earned its certification, it may not be the best place to certify your torque tools.
If it has been more than a year since your torque tool has been calibrated, schedule it now.
– Most torque instruments have a factory calibration recommended interval of one year.
Estimate the number of cycles your torque tool uses each month.
– Remember, each “click” of a wrench constitutes a cycle. How many lug nuts do you tighten in a day/week/month? Many torque instruments may need to be tested multiple times per year depending upon their usage.
Before and after every use, make a visual inspection.
-Look for any signs of damage, wear or deterioration. If you know that the tool has been dropped, it is certainly time to have it tested.
Consider how your torque tools are stored.
-Storing the torque wrench in high humidity conditions will lead to corrosion in the tool. Storing "click" style torque wrenches in any setting besides the lowest one will cause main spring wear and failure.
Maintenance costs less than replacement.
– Most quality torque tools can be maintained/repaired at time of testing and calibration. Properly maintained and regularly calibrated torque tools can be used to provide accurate repairs for decades.
When in doubt, send it out. –It only takes a few days for an efficient lab to turn around your torque tool for testing, repair and calibration. If usage, time or any considerations cause you to doubt its accuracy, have it picked up and sent out for testing. The cost of maintaining the tool is far less than the liabilities associated with doing the repair over again or worse, a wheel coming loose.
Demand a traceable certificate of calibration.
–This means there is an unbroken chain of traceability through NIST to the highest-level international standards possible. At some point in your career, there may come a request to verify the accuracy of your torque tools. These requests are typically the result of a legal inquiry. Simply put, when you pay to have your torque tools calibrated you need to know with absolute certainty that the measurements are performed using 100% traceable and compliant equipment. This is what we do – we can help.
Remember, critical installation success starts and ends with torque tool certification.
Mark Anderson – Experienced and Honest Owner and CEO
Dedicated to Excellence, Quality, Customer Service, and Leading by Example
Our 4 Core Values: Higher Expectations, Innovative Geekism, Fun & Fair, Urgency for the Customer
Team Torque Inc. @teamtorque
For more information on a custom VIP Torque Program - contact us directly - 1-701-223-4552
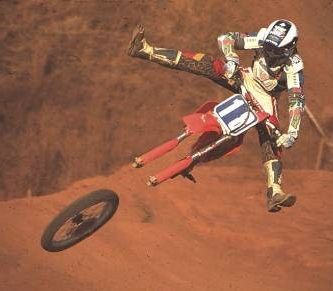